Machine range
Bending and prebending machines
AMB PICOT has 150 years of expertise in the design and manufacture of plate bending machines.
Over the years, AMB Picot has enriched its range to adapt to its customers’ technical requirements, manufacturing two-, three- and four-roller bending machines.
All of its plate bending machines can be equipped with numerical control systems that give operators the power to perform very precise bending.
Bending at pace!
- Capacity: 0.2-8 mm (steel S235)
- Usable length: 0.5-2 m
Versatility and performance
- Capacity: 0.5-40 mm (steel S235)
- Usable length: 1-6 m
Thick materials without compromise… but not only that!
- Capacity: 0.2-8 mm (steel S235)
- Usable length: 0.5-2 m
Your custom bending
- Two, three or four rollers
- Capacity: 0.5-40 mm (steel S235)
PICOT PIONNIER DU ROULAGE DE TÔLE ÉLECTRIQUE
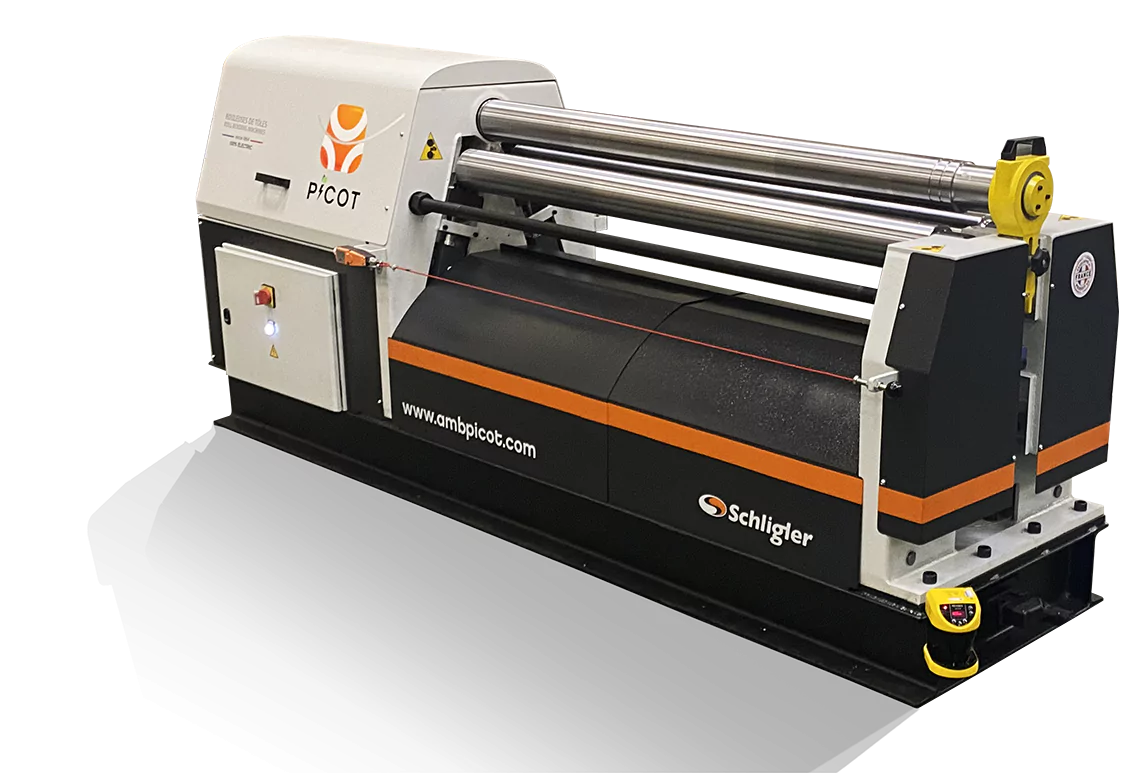
ELECTRICAL machines range
Bending and prebending machines
- -80% reduction in consumption
- Accurate to 1/100th
- Clean and quiet
- Simplified maintenance
With Easyroll I didn’t take 1 step forward, I took 1000!
M. Ballon – MB Technique R3h170-20@2022)
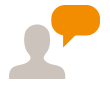